Alternative of Methylene Dichloride for Polyurethane Slabstock Foam
Wu Bin
OSiC Performance Materials
Urethane Additives
No.1218, Songsheng Road
201600 Shanghai
China
Polyurethane polyether slabstock foam is the largest type of polyurethane soft foam, which is generally produced by continuous process, including trough and liquid lay-down(LLD) foaming systems. In the production process, methylene dichloride ( MC ) is a commonly used as foaming agent.
1. MC has three functions in the production process of polyurethane polyether slabstock foam : the first is to absorb the reaction heat, the second is to assist foaming, and the third is to clean the pipeline after production.
1.1 We know that the molecular weight of water is 18, and the exothermic heat of water and TDI chain growth is 188KJ/mol. The exothermic heat of water is 10.4KJ/g, and the endothermic heat of MC vaporization is 0.34KJ/g, the ratio of the two is about 30. The above is just to let us perceptually understand the influence of MC on the heat of reaction. In fact, the mechanism that affects the reaction heat is very complicated, and is related to factors such as the heat release rate, methane concentration, and methane gasification rate in the formula. Each factor is a complex variable.
1.2 The increase of MC will obviously increase the elongation of the foam, but it will not necessarily increase the tear strength of the foam. Foam that is easy to stretch does not mean that it is not easy to tear. The increase of MC will reduce the degree of internal temperature rise during the foam reaction, which is not conducive to the formation of hard segments, so the addition of MC will easily make the foam soft and feel elastic to the touch. But this kind of foam that feels elastic, its falling ball rebound is not very high.
1.3 Since MC is a good solvent, at the end of production, using MC to clean the pipeline can avoid quality problems that may occur in the next foaming process.
Therefore, methylene chloride is a cheap and efficient choice in the production of polyurethane slabstock foam.
2. However, MC is also a dangerous substance, and its dangers are shown in:
2.1 Flammability: Although it is not flammable under normal temperature and pressure, once heated, MC is still quite dangerous: it is flammable when exposed to high heat from an open flame. Decomposition by heat can emit highly toxic phosgene. Combustion (decomposition) products: carbon monoxide, carbon dioxide, hydrogen chloride, phosgene.
2.2 Environmental hazards: It may be harmful to the environment, accumulate in groundwater, harmful to aquatic organisms, and is a potential source of dioxin release in the atmosphere. Therefore, methylene chloride was included in multiple controlled lists in 2018-2019: Toxic Harmful Air Pollution (2018), Toxic and Harmful Water Pollution (2019), List of Priority Control Chemicals (2018).
2.3 Health hazard: It has anesthetic effect and mainly damages the central nervous system and respiratory system. Dichloromethane was listed as a 2A carcinogen by the WHO in 2017 and has the risk of teratogenicity.
Therefore, it is urgent to replace MC in the production process. In Europe, although the EU does not prohibit the use of dichloromethane, at the national level, many countries have set very low levels of methylene chloride emissions, which in fact are disguised as prohibiting the use of dichloromethane. From IKEA product standards (IOS-MAT0010 / 35 page, IOS-MAT0054 / 12 page), we can see that methylene chloride has been listed as a prohibited substance.
3. In European and American countries, alternative MC has mature industrial applications, and we can solve this problem in many ways.
3.1 Super Soft Polyether Polyol Technology: Super Soft Polyether Polyol is a type of polyether polyol with a special structure, including Dow, Covestro, BASF and domestic manufacturers have similar products. But from the current point of view, due to the difference in mechanism, its feel is still significantly different from that of MC.
3.2 Softener functional additives technology : OSiC's NOVAX SF-360/365 forms the hard segment area through hydrogen bonding, and the soft segment is randomly wound to form the soft segment area. Ordered polyurea precipitation is reduced, the degree of microphase separation is improved, the rigidity is enhanced, and the softness is increased. And the elasticity decreases. For details, please refer to:
NOVAX SF-360 softener replacing methylene chloride in flexible polyurethane foam - Solutions - OSiC Performance Materials (osicgroup.com)
3.3 Antioxidant technology : since MC can effectively take away heat, it is an inevitable choice to adopt effective antioxidant technology after replacing MC. Nowadays, various companies generally adopt composite antioxidant technology, that is, compound anti-heat oxidant, anti-ultraviolet absorber, anti-radical absorber and so on. Including: hindered phenols, hindered amines, phospholipids, imidazole ring and other structures. Suppliers include: BASF of Germany, Chengbei Chemical of Japan, etc. However, since antioxidants are generally expensive, they will increase production costs.
3.4 Liquid carbon dioxide foaming technology: Carbon dioxide foaming technology has been widely used abroad. The use of carbon dioxide has the following advantages:
( 1 ) Carbon dioxide is a colorless, odorless, non-toxic, harmless, stable and flame retardant gaseous substance.
( 2 ) The heat of vaporization varies between 0.250-0.350KJ/g according to pressure and temperature. It has a similar mechanism as MC, which can quickly remove heat during production to obtain soft foam.
( 3 ) Comply with the national policy of reducing carbon emissions.
( 4 ) The expansion ratio is 3.2 times that of methylene chloride, but the production cost is lower.
4. Below we will introduce the carbon dioxide foaming technology in detail.
According to the information currently available, in North America ( including the United States and Canada ), a total of up to 36 factories using carbon dioxide foaming technology to produce continuous foam. Of the 36 factories, 29 use the Sieves system and 7 use the gatebar system. What is sieves system and what is gatebar system ? What are their differences?
The Sieves system is the production system used by Ladderberg and Hennecke ( pictured below )
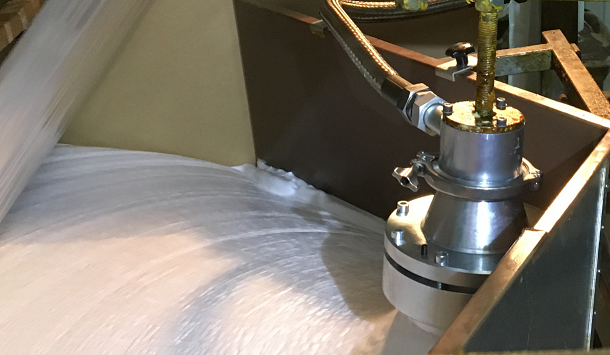
Because the pressure of carbon dioxide foaming is much higher than that of ordinary foaming, at the same time, in order to avoid the influence between the pores, a multi-layer composite technology is used to install a screen on the part of the foaming head. Different specifications of screens were used according to the viscosity of the material, the proportion and the amount of POP added. Generally speaking, a single-layer screen cannot achieve the purpose, and a multi-layer screen is generally used in combination. The form of the screen is as shown in the figure below:
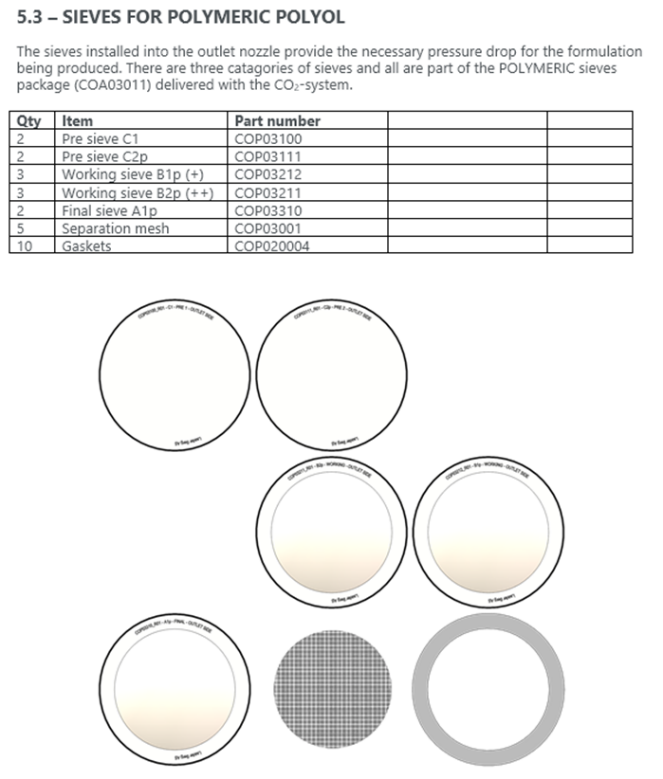
The Gatebar system is a production method adopted by Cannon Viking. It is a bit similar to the head swing in the foaming process, but it does not move. This production method eliminates the problem of porosity, but brings new troubles. The edges are prone to defects. Perhaps this is also the reason why the factories using this production method are far smaller than Sieves.
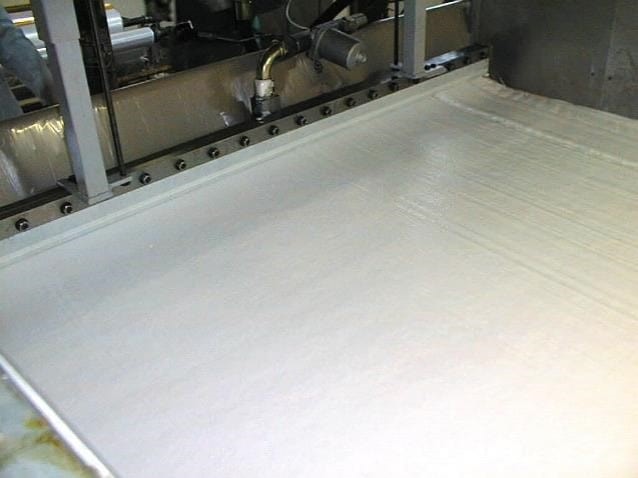
5. Thanks to the support of Ladderberg, we take the Sieves system as an example to briefly describe the foaming equipment and related processes
As shown in the figure below, similar to normal polyurethane foaming equipment, the materials used include polyether polyol, white oil, and TDI. Other raw materials include liquid carbon dioxide, super soft polyether and nitrogen. As we all know, liquid carbon dioxide can be dissolved in polyether polyol. According to known data, at 8000Kpa, 1 part of liquid carbon dioxide can dissolve 0.17 part of polyether polyol. As the pressure increases, the solubility will decrease, but the overall data is 0.05W polyol/1W CO2. Therefore, the liquid carbon dioxide also acts as a solvent, reducing the viscosity of the system and helping to mix with TDI. One more thing, liquid carbon dioxide and TDI have no solubility relationship.
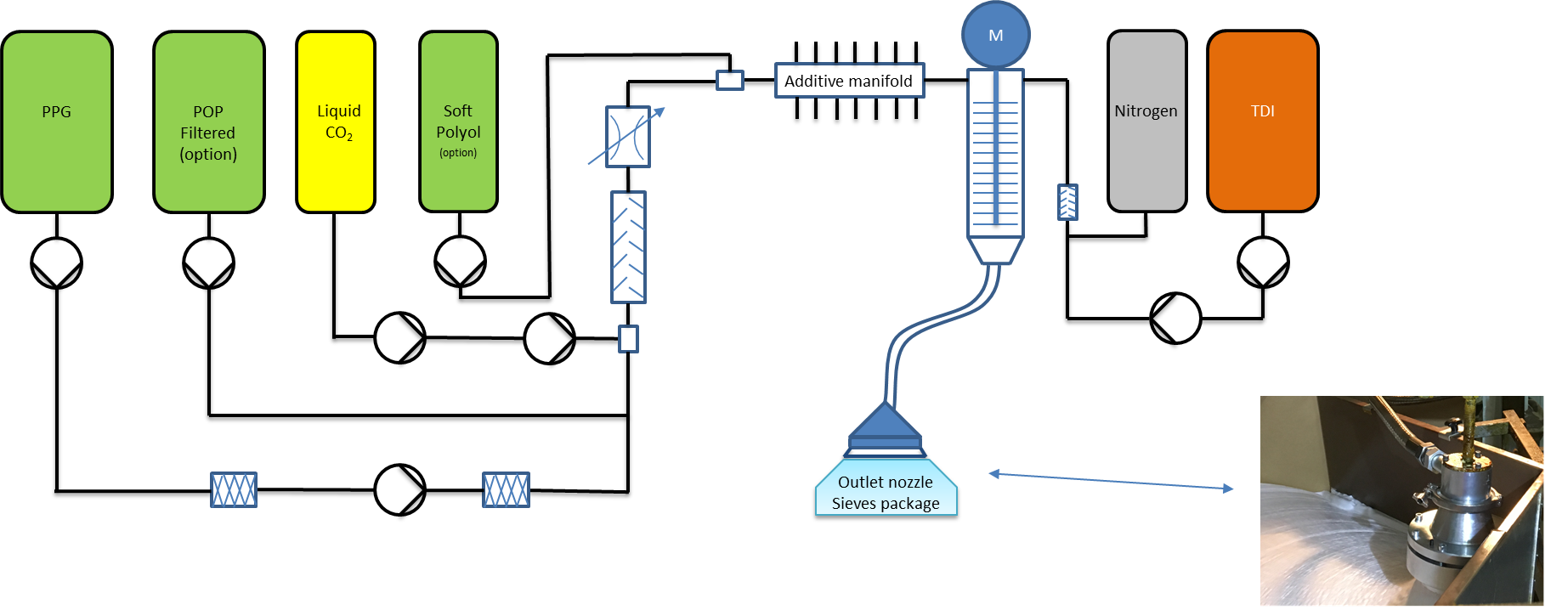
( Flow chart of carbon dioxide foaming system )
The temperature of carbon dioxide used here is -25 degrees Celsius and the pressure is 17 bar. Someone may ask whether this is supercritical carbon dioxide. My answer is: no. To understand the carbon dioxide system, take a look at the following phase diagram.
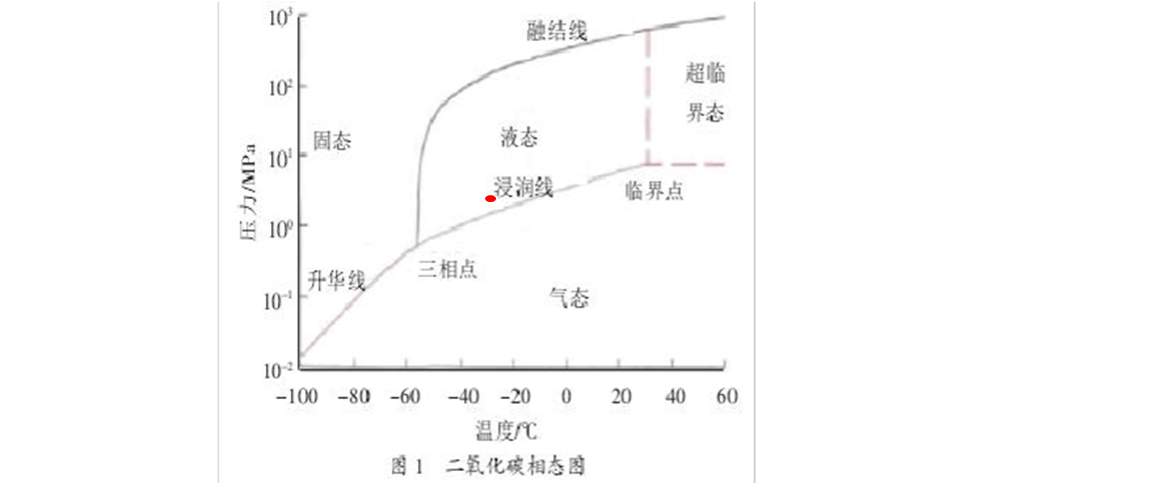
(Carbon dioxide phase diagram)
The position of the red dot is the temperature and pressure point used by the system. The advantage of this choice is that the energy demand is the lowest, and the pressure drop can quickly vaporize. Next time, if someone says to use a supercritical system, you can ask him what the pressure and temperature are and you can easily judge. In addition, it can also be seen from the foaming photos that there is no traditional foaming clearing section, which is also the difference from traditional foaming.
Both PPG and POP used in the system require high pressure, which is also to maintain the liquid state of carbon dioxide. For POP, because it contains polystyrene particles, it is necessary to choose products with a small particle size. We recommend using Shell’s SP30-45F or Covestro’s 1159S to avoid affecting the screen. Because in the production process, there is no way to replace the screen, and there is no way to use a pressure regulating valve to control the pressure like traditional foaming. Therefore, once blockage occurs, it can only be shut down, causing losses.
The super soft polyether and additives used require a semi-high pressure system, and any fillers are prohibited for the same reasons as above. Therefore, the use of carbon dioxide foaming system can only use Milliken's reactive colorants, and traditional color pastes and toners cannot be used. Fillers and melamine cannot be used in the formulation.
Due to the addition of carbon dioxide, the HLB value of the system has greatly changed. Traditional silicone oil cannot be used. It is necessary to replace the silicone oil for carbon dioxide foaming. OSiC has related silicone oil products to choose from. Other raw materials are not much different from normal foaming technology.
Isocyanate TDI requires the use of a high-pressure system. The use of high-pressure nitrogen (20Mpa) as the gas source also takes into account the compatibility of carbon dioxide. It is not recommended to use compressed air.
In addition, in the production process, because the sieves system has different options for different formulations, it is not possible to change the formulation during the foaming process like traditional foaming. The same formula is only possible to adjust the ratio, but it can only be adjusted from a small flow rate to a large flow rate.
6. Summary
Carbon dioxide foaming replaces toxic methylene chloride, while using greenhouse gas (carbon dioxide), in line with the national strategy of energy saving, emission reduction, and carbon emission reduction. And it has the irreplaceable advantages of high foaming ratio (3.2 times of methylene chloride), wide density range (above 14KG/M3), low cost, finer and more open cell structure. Of course, there are disadvantages, including high-pressure system maintenance, restricted formula replacement, restricted POP and colorant options, and unavailability of fillers. China is one of the main production bases of polyurethane slabstock foam in the world. Although carbon dioxide foaming technology has been widely used abroad, no manufacturer in China has yet to use this technology. We believe that in the near future, we can see the first domestic manufacturer to use carbon dioxide foaming system to produce polyurethane slabstock foam.
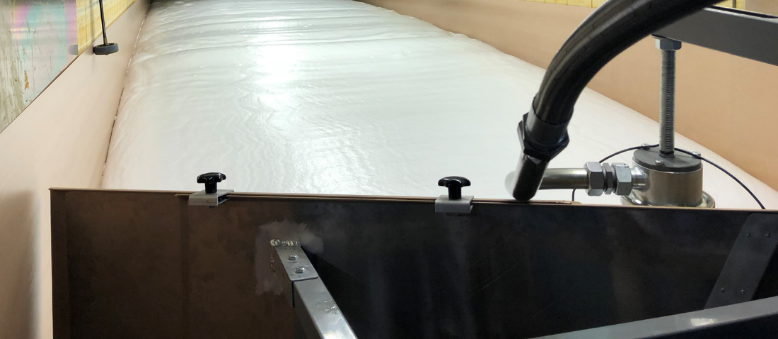
( Carbon dioxide foaming scene photos )
7. Thanks
Finally, we would like to express our gratitude to the Ladderberg company that provided relevant information. Ladderberg is a manufacturer specializing in the production of flexible polyurethane foam foaming equipment. It has sold more than 550 foaming equipment in 90 countries around the world. The carbon dioxide foaming system can be embedded Installed in the Ladderberg foaming system to achieve automatic and precise control. If you have any questions about the carbon dioxide foaming system, please feel free to contact OSiC (info@osicn.com.cn). We will serve you wholeheartedly.
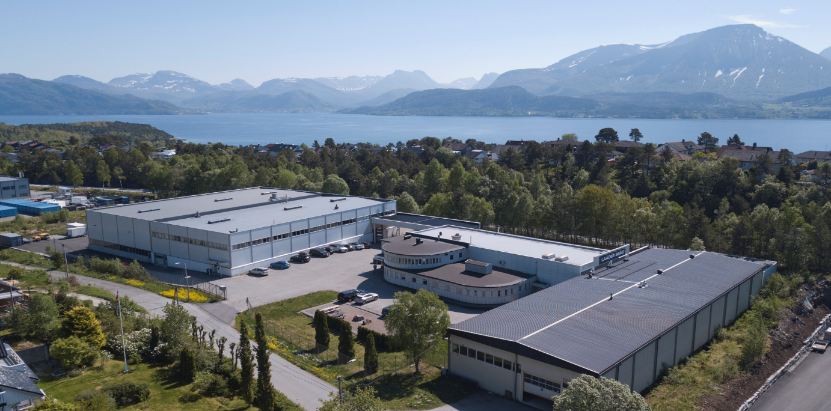
BIOGRAPHIES
Wu Bin
Born in 1978, Bachelor of Fine Chemicals from East China University of Science and Technology, Master of Economics from Shanghai University of Finance and Economics. In 2000, Wu joined the Shanghai Institute of Organic Chemistry, Chinese Academy of Sciences, engaged in organic synthesis, participated in and completed the National Natural Science Foundation of China (new drug synthesis) and the National Defense Science and Technology Commission (organic silicon materials). Wu joined GE Toshiba Silicone(later Momentive) in 2004 to work in technical research, project manager, and factory director. In 2010 he joined OSiC and presided over the construction and operation of Songjiang and Zhangjiagang factories. In 2020, Wu began to serve as the principal of the academy of OSiC.
TOP